Bergeron Centre for Engineering Excellence: Lassonde School of Engineering
Certifications & Awards
Project Team
- Project Owner: York University
- Architect: ZAS Architects + Interiors
- Engineer: Arup
- Landscape Architect: Scott Torrance Landscape Architect Inc.
- Construction Management : Laing O'Rourke Canada
- Sustainability : Zon Engineering
Green Building Audio
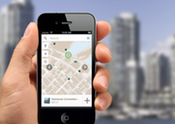
Our audio tours qualify.
Get one today!
Bergeron Centre for Engineering Excellence - York University Construction PM Irina Arsene & Paul Stevens of ZAS Architects
Summary
York University has instituted a new Engineering Building in Toronto, Ontario. The $113 million Bergeron Centre for Engineering Excellence is the new home of the Lassonde School of Engineering, which aims to instil engineers with entrepreneurialism, social conscience and a sense of global citizenship. Located in the southwest quadrant of York University’s Keele campus, the 170,000 square foot (15,800 square metre) building consists of five stories to accommodate learning spaces for electrical, civil and mechanical engineering programs. The facility embraces 21st century learning by providing spaces that are flexible, bold, creative, and collaborative.
Highlights
• High performance building enclosure with high insulation levels in the
roof, walls and floors
• Low flow rate fixtures: 4.8 LPF toilets, 0.5 LPF Urinals and 1.9 LPM
lavatory faucets
• Vegetated roof on over half of the building roof
• Low window-to-wall ratio for superior energy savings
• Building design features minimize risk for migratory bird collisions
• Half of the project’s wood products originate from sustainably managed
FSC supply chains
• Materials used in the building’s construction sourced from local
manufacturer’s with a high percentage of recycled content
• Superior indoor air quality
The Lassonde School of Engineering has no lecture halls. Instead it hosts 18 teaching labs, 8 active learning labs as well as design workshops, studio and social spaces for undergraduate, graduate and post-graduate students, researchers and faculty to interact in an innovative and supportive learning environment.
Overlooking the Stong Pond and Arboretum to the south and west, the building’s upper levels host the electrical and mechanical engineering departments, with the civil engineering program rooted on the lower levels. Student services are located at the school’s entrance with faculty administration at mid-level for optimal accessibility and engagement between faculty and students.
Sustainable Sites
Part of what makes a building green is its location and surroundings. Integrating the site within local systems of transportation, amenities and reducing its impact on other natural systems are key to appropriate and green design.
The Lassonde School of Engineering was constructed on previously developed land amid the highly dense and generous amenities of the York campus.
Sustainable Transportation
In tandem with the construction of this project comes the long-anticipated Spadina Subway Expansion to York University. Completion in 2017 will provide optimal sustainable transportation and connectivity to the campus, which already enjoys frequent public bus service.
Rainwater Management
Managing the precipitation that falls on a site is important to control rain flow to prevent flooding and mitigate the impact on municipal infrastructure. To deal with rainwater falling on site, the project created two storm water management dry ponds. These retain runoff and control outflows for the 2 through 100-year storm events. Outflow from the first pond, which has a volume of 1,395 m3, is sized to control peak flows to the existing Stong Pond located on campus. Flows in excess of the 100-year storm event will exceed the capacity of the two ponds, which has a combined volume of 1,618 m3 in total, and overflow directly to Stong Pond.
To treat the captured rainwater, an oil/grit separator removes approximately half of the Total Suspended Solids (TSS) from the water. An infiltration trench located downstream of the dry pond removes 70% of the remaining solids, for a total TSS removal effectiveness of 85%.
Green Roof
Half of the project’s roof is covered with a vegetated ‘green’ roofing system, which further assists in diminishing the rainwater peak flow rate, as the vegetation soaks up rainwater and releases it far more slowly than a conventional roof to reduce the strain on campus and municipal storm water systems. The green roof also protects the roofing system membrane from wear due to exposure of the elements and prevents the roof from excessive solar heat gain.
In a similar effort to mitigate a hot urban microclimate, which stems from the heating up of dark materials such as asphalt, the surrounding hardscape was specified to be a light-coloured material for a high solar reflectance to combat the heat island effect.
Reducing Light Pollution
In the evenings, exterior LED fixtures have been installed with full cutoff features to shield the lighting from spilling into the night sky in an effort to reduce light pollution. Interior lighting is controlled via ceiling and wall mounted occupancy sensors which are also tied into the building automation system for after-hours shut-down. This further increases the energy savings for the project while simultaneously reducing light spillage from inside the building.
Water Conservation
As a means of prioritizing potable water savings, the project committed to foregoing the installation of a permanent irrigation system for plantings around the building’s perimeter. To ensure the success of these plantings without irrigation, the design team utilized drought-tolerant landscape, incorporating native plantings, which also require less maintenance.
Note: The City of Toronto has published a resource on drought tolerant landscaping with a list of drought tolerant species.
Inside the building, the toilets use only 4.8 liters per flush (LPF), with urinal flow rates at 0.5 LPF. The washroom faucets use 1.9 Liters per minute (LPM) with auto controls for greater efficiency. Kitchenette faucets and showerhead have a flow rate of 5.7 LPM. The use of these high efficiency fixtures results in potable water savings of 35% compared to a model with conventional fixtures and flow rates.
Energy
Before any of the energy systems are determined and sized, the building envelope must be designed for high thermal insulation with optimal components for energy savings. The Lassonde School of Engineering prioritized a high performance building enclosure with high insulation levels in the roofs, walls and floors.
Windows in the project were also specified to be high performance with low-e coatings to suit the building orientation. Because windows can be the lowest thermal performer in a wall assembly, the project prioritized an overall low window-to-wall ratio in the design to minimize energy use and losses.
The HVAC system incorporates energy recovery, using heat recovery wheels for heat exchange. These air-to-air heat exchangers can recover energy from both heat and moisture. An airside economizer is used where the air-handling units draw outside air and exhausts return air to lower cooling needs and costs during temperature shoulder months.
The building is mechanically ventilated to take advantage of efficiencies using a Variable Air Volume (VAV) system. VAV systems meets the different heating and cooling needs of the project’s various building zones through modulating dampers, varying the airflow for more precise temperature control, lowering fan energy consumption and providing passive dehumidification.
Variable Frequency Drive (VFD) fans allow the system to run more efficiently by using lower frequency and voltage for less motor energy use as well as less wear and tear. Heating and cooling loads are reduced by using supply air temperature reset controls to match capacity with actual loads, thereby providing more precise levels of control applications.
CO2 sensors were installed to control ventilation in various densely occupied spaces such as classrooms, meeting rooms, computer labs, and multi-use assembly/conference rooms, balancing the ventilation rate with energy efficiency depending on occupancy.
The project opted for condensing hot water heaters to deliver a more efficient form of heat exchange compared to a traditional boiler. The water vapour created when gas burns in the boiler condenses to release latent heat, which is a significant source of energy. Condensing boilers can have efficiency ratings up to 98%.
Lighting design
The lighting design for the Lassonde School of Engineering contributed to overall energy savings by reducing interior lighting power density and using low exterior lighting power. The utilization of occupancy sensors in most spaces and daylighting sensors in some perimeter spaces creates energy savings through smarter lighting practices where spaces remain unlit if unoccupied or provided with sufficient day lighting.
An Energy Management and Control System (EMCS) controls building services systems to operate at their optimum performance. The system monitors energy consumption to ensure maximum efficiency.
The EMCS is compliant with the data communication protocol for Building Automation and Control Networks, known as BACNet, set out by ASHRAE. Using direct digital control (DDC) technology, the EMCS controls the major mechanical equipment that do not have factory-supplied controls and integrates with mechanical packaged equipment to allow monitoring, set point adjustment, and trending features as well as basic adjustments.
Operations staff can use the trending features to build historical data of system elements to allow for continuous optimization and fine-tuning.
The building’s EMCS presents a valuable research and learning tool for students who, with the appropriate access protocols, can investigate and study the energy usage and operation of the building services systems, without having access to change any of the building set-points.
Materials and Resources
The prioritization of use of materials originating and manufactured within shorter distances to the project decreases the transport energy required to deliver to site. Local material use was targeted and tracked throughout the project to achieve over 34% of the construction materials came from within 800 km of the project.
The project strived to source and install recycled building materials wherever practicable. Recycled materials that could be sourced with minimal to no incremental cost were identified early in the project, and include materials such as structural steel, cast-in-place concrete, gypsum board, carpets, concrete blocks and unit pavers, and steel studs and doors. Over 22% of materials that were sourced contain recycled content.
To demonstrate support and demand for wood products originating from sustainably managed forests, over 50% of the wood products installed on site were sourced from Forest Stewardship Council (FSC) supply chains.
Construction practices are making gains towards greater coordination of construction waste whereby recyclable materials are separated to divert as much tonnage from the landfill as possible. This project created construction waste management practices that resulted in a 90% diversion of waste from landfills.
Indoor Environmental Quality
Healthy indoor air quality is essential for occupants to focus within learning environments. The design team prioritized a superior air quality throughout the design, specification and construction phase of the Lassonde School of Engineering project. All adhesives, sealants, paints, and coatings utilized within the building envelope on site had to conform to low Volatile Organic Compound (VOC) emission standards. Likewise, all flooring systems had to meet or exceed high industry standards from FloorScore and CRI Green Label, and all composite wood products had to be free of toxic urea-formaldehyde.
For further safeguarding of air quality during construction, trades upheld air quality protection standards put forth by the Sheet Metal and Air Conditioning Contractors’ National Association (SMACNA). Upon the project’s substantial completion and prior to occupancy, a building ‘flush out’ was scheduled to ventilate the building at the project’s most intense period of contamination with and to push out residual construction debris, particles and volatile organic compounds responsible for that ‘new building smell’.
To maintain a comfortable indoor environment for the building occupants, the building systems were designed to maintain specified indoor conditions that are set out by the ASHRAE 55-2004 Thermal Comfort Conditions for Human Occupancy. A permanent monitoring system was installed to verify that these conditions are met and an occupant thermal comfort survey will be conducted 6 to 18 months after the building is occupied.
Sources:
toronto.ca/1