MNP Tower - 1021 West Hastings
Certifications & Awards
- LEED Canada for Core and Shell Development (registered)
Project Team
- Geotechnical Engineer: Geopacific Consultants Ltd. & Golder Associates Ltd.
- Building Science Professional: Morrison Hershfield
- Commissioning Authority: CES Engineering Ltd.
- Structural Engineer : Read Jones Christoffersen
- Landscape Architect: Durante Kruek Ltd.
- Energy Engineer: Integral Group
- Civil Engineer: Keystone Environmental
- Electrical Engineer: Schenke Bawol Engineering Ltd.
- Mechanical Engineer: Integral Group
- LEED Consultant: Integral Group
- Contractor: Ledcor Construction Ltd.
- Architect: MCMP Architects
- Client/Developer: Oxford Properties Group
Green Building Audio
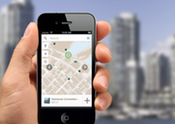
Our audio tours qualify.
Get one today!
Summary
MNP Tower at 1021 West Hastings Street is a 37-story ‘A’-class office tower by Oxford Properties. Located on West Cordova Street, MNP Tower stands immediately adjacent to the well-known Guinness Tower office building on the west and the iconic Marine Building to the east, with Oceanic Plaza across the street. This cluster of buildings comprises Oxford Plaza and are newly linked via an underground concourse with upgraded amenities.
Green Building Project Highlights
-
Electrical refuelling available in 74 parking spaces
-
Durable Building plan implemented with careful attention to building envelope details and assemblies during design and construction for a long-life building
-
No boilers or chillers: spaces conditioned with distributed, zone-level fan coil system and Variable Refrigerant Flow (VRF) systems on each floor
-
Optimized use and tracking of regional materials and Forest Stewardship Council (FSC) certified wood
-
Energy performance measured and verified after one year with real data compared to a calibrated project energy model for exceptional troubleshooting
-
Lighting Power Density reduced through optimization of natural light, occupancy and daylight sensors, efficient fixtures and low voltage controls
Project Description
The MNP tower’s exterior demonstrates a unique profile. Shaped like ‘a glass talon’, a slight area increase is visible in the southeast portion of the building with each consecutive floor, creating a variation in square footage from floor to floor.
The curved roof screen concept extends beyond the 37th floor, with an apex height of approximately 521 feet. The first three levels (level 1, mezzanine level and level 2) consist of commercial retail units, with the remaining 35 levels hosting open office space. Beneath the building, there are four levels of underground parking and one level for mechanical and electrical services.
Sustainable Sites
MNP Tower was built on a previously developed site. Urban infill projects such as this minimize a development’s impact by avoiding greenfield sites and creating additional density for occupants’ ease of use.
The project was decisively built in a prime downtown location with the occupants in mind. The compact urban harbour-front environs provide access to a number of nearby community services. MNP Tower is within a short walking distance to a waterfront park, numerous eateries, commerce and convention centres. The project’s underground concourse lends easy accessibility to a restaurant, fitness centre and ample bicycle parking between the three Oxford Properties buildings.
Access to alternative transportation at the MNP Tower project site is premiere. Waterfront Station is one of the city’s major light rapid transit hubs, which is located only 450 meters away from MNP Tower. It provides links to the Canada Line, Millennium Line and Expo Line Skytrain, as well as Seabus ferries to North Vancouver. There are high frequency bus lines that travel past the project, and the availability of car-share vehicles such as Modo, Evo, Zipcar and Car to Go, is rapidly growing in this downtown area.
MNP Tower is well connected to the City of Vancouver’s network of cycling infrastructure, which includes separated bicycle lanes to encourage occupants to utilize cycling as a viable mode of commuting.
These readily available options make it easier for occupants to reduce their transportation-based carbon footprint.
For those that drive to MNP tower, there is preferential parking for high occupancy vehicles, which is equal to 5% of parking spaces. To future proof the parking area and to encourage the uptake of low-emitting and fuel-efficient vehicles, like electric cars, the project provided refuelling stations equal to 3% of vehicle parking.
Occupants will be able to choose from 74 electric re-fuelling receptacles on Level 1, which are pad-lockable. There are 5 parking spaces with electric refuelling, which are reserved for e-vehicles only. The additional 69 stalls have display signs that read “Electrical Refuelling Available”.
Heat Island Effect - Non Roof
All parking for MNP Tower is located beneath the building. Underground parking not only provides efficiencies for building layout and design, it also provides the added ecological benefit of avoiding additional asphalt surface construction in the downtown area, which heat up and create urban microclimates known as ‘heat islands’. Heat Island effect can negatively impact air quality, flora and fauna habitat, as well as increase solar heat gain, leading to energy demand increases and greenhouse gas emissions through mechanical cooling in nearby buildings.
Water Efficiency
Imagine the impact of a 37-story building opting for low flow water fixtures. Compared to an equally occupied building with conventional fixtures, MNP tower saves over 4.7 million litres of water every year1. That’s enough water to grow the food for a family of four for over half a year2.
Energy and Atmosphere
Optimize Energy Performance
Key decisions were made for optimal energy performance at MNP Tower. The design team prioritized upgraded insulation values in the roof, walls and glazing for better building envelope performance, as compared to a conventional tower. To reduce solar heat gain and demand for cooling, exterior shading in the form of 6” vertical fins were installed on the south, and west façades; the east face was finished with 3” vertical fins and with a canopy on the first floor.
The project significantly reduced its electricity use for domestic hot water, heating and cooling, and internal lighting. The sum of these energy conservation measures yielded a 35% energy reduction by cost, when compared to a baseline building model design conforming to ASHRAE 90.1-1999 standards.
For lighting, the overall lighting power density (LPD) was reduced through a number of measures, including the use of occupancy sensors in the parkade, restrooms and electrical/mechanical room, and daylight sensors in perimeter office zones. All luminaires were selected with attention to low operating costs and high efficiency. And, with the exception of emergency lighting and some locally switched lighting, all lighting is controlled by a TLC computerized low voltage lighting control system, which uses low voltage manual switches, occupancy sensors, and daylight sensors for greater efficiency.
Heat recovery ventilators (HRV) are located in the washrooms on each floor and serve as the primary ventilation source. HRVs take advantage of ‘waste heat’ by utilizing a double fan system, mixing stale, outgoing air with fresh outdoor air. With a heat recovery effectiveness of 57%, these HRVs save considerable energy.
Space heating and cooling are provided to a distributed, zone-level fan coil system. The system uses Variable Refrigerant Flow (VRF) systems located on each floor.
VRF systems allow for accurate, individualized temperature control to each unit using a refrigerant-based system. These fan coil units are tied to separate local thermostats to allow user control for comfort needs. The use of this system also eliminated the need for a central hydronic plant and provides energy savings as compared to a packaged rooftop heat pump.
By using low-flow domestic hot water fixtures, MNP Tower not only saves water, but the 43% reduction in flow creates energy savings by heating less water.
Based on design, the operational systems in MNP Tower, such as heating, ventilation, air conditioning (HVAC) and lighting, save 383 tons of CO2 a year, as estimated using Environment’ Canada’s Inventory 1990-2002 Data (with an adjustment factor for line losses and upstream emissions).
Measurement and Verification
To ensure the building’s systems operate to their optimal efficiency, MNP Tower has implemented a Measurement and Verification (M & V Plan). Measurement and verification substantiates the energy conservation measures implemented and equips facility managers with much-needed tools for operations. Meters were installed to monitor end uses in the building, with data and trend logs recorded over a one-year period. Using a calibrated energy model with actual weather data and occupancy fluctuations, the building’s performance relative to its original modelled potential is verified. The results of these models are compared for discrepancies between anticipated and actual usage to identify under-performing areas, and to make improvements and modifications. Measurement and Verification is a valuable addition to the project’s building commissioning process.
Commissioning provides assurances that building systems are initiated to operate as intended, and facilities staff is trained, which can avoid operational problems, as well as facilitate improved communication and reduced change orders during construction3.
Materials and Resources
The type of building materials used, where they originate, and how they’re disposed are kept front of mind by the design and construction team during specification and installation as a means to create a building of lower impact. The use of materials that are recycled, harvested and produced within the local region and/or from natural materials are prioritized and incentivized in the LEED certification system. Close to 25% of materials were recycled and roughly 40% of building products were harvested, extracted and manufactured within a 800 km (500 mile) radius.
A waste management plan was implemented during construction. The weight of materials diverted from the landfill were tracked and recorded to achieve diversion rates 75% or higher.
Forest Stewardship Council Certified Wood
MNP Tower and Oxford Properties committed to supporting sustainable forestry practices by installing wood products from sources with Forest Stewardship Certification (FSC). The project went well beyond the 50% value outlined by LEED rating system, installing a total of 80% of wood products by dollar value. FSC is the only wood product certification that protects rare and endangered forests and wildlife, as well as the rights of aboriginal peoples and Oxford Properties demonstrated their commitment to these practices.
Durable Building
For a building’s ‘skin’ to perform well, it must be designed for thermal and moisture performance, with attention to the air-barrier system and resistance to mould. Building codes do not currently provide enough specifics for building durability. Fortunately, a number of envelope failures can be prevented at the design and construction stage. To this end, MNP Tower worked with a building envelope consultant to create a Durable Building plan for a long-life building envelope with attention to building details and assemblies during design and construction.
Indoor Environmental Quality
Superior indoor air quality is of great value to an office environment. Occupant health and well-being and potential productivity levels are directly affected by the quality of the indoor environment, and integral to what makes a building green. The owners of MNP Tower recognize the value of occupant comfort for tenant satisfaction and have implemented a number of measures to ensure a healthy indoor environment.
When the occupants of MNP Tower move in, they won’t be met with a chemical smell conventionally associated with new construction and renovations. When paints, carpet materials and glues give off a smell, it indicates the off-gassing, of high levels of Volatile Organic Compounds (VOCs). MNP Tower ensured the use of low-emitting paints, adhesives, sealants, as well as composite wood products, based on industry standards. Low ventilation rates and/or high occupancy spaces can result in high carbon dioxide levels, which have been associated with side effects like sluggishness, and reduced focus and decision-making performance. The heat recovery ventilation units on each floor of MNP Tower monitor carbon dioxide levels; if CO2 levels increase to 800 ppm, the supply and return fans switch to high speed, and the return air damper opens. Thermal Comfort Compliance and Monitoring
The HVAC design of the project meets thermal comfort requirements of the industry standard from ASHRAE (55-2004), addressing interior air factors such as temperature, air speed and humidity and ensuring these factors stay within a prescribed range. In the interest of confirming occupants are satisfied with the space conditioning in the building, a process was put in place to survey occupants to provide important feedback to building owners and facility managers.
Daylight and Views
The quality of an indoor space is essential for occupant comfort and how well they are able to perform in the space. Occupant access to outdoor views have been linked to productivity as well as relief of boredom, anxiety, and stress.
Building occupants also overwhelmingly prefer working near windows. The variety and stimulation that natural lights provides cannot be overstated, and more research is showing that increased levels of daylight, with the right controls against glare, may be critical to reducing stress levels and may improve employee performance. Taking advantage of natural light as a resource is also a potential means to reduce energy use for electrical lighting4.
Notes:
-
Water savings based on LEED WEc3 template. ↩
-
About 6,800 gallons (25,740 liters) of water is required to grow a day’s food for a family of four. www.seametrics.com/blog/water-facts ↩
-
www.energy.wsu.edu/Documents/BuildingCommissioning.pdf ↩
-
www.wavefcm.com/Attachments/4_Why_Daylight_and_Views_Matter.pdf ↩